Posted on April 3, 2019 in Cars.
Jaguar Land Rover gives aluminum a second life
Jaguar Land Rover is taking a new step in its strategy for using aluminum in a closed circuit. A bold recycling program is in place with the goal of transforming the cars of today into the vehicles of tomorrow. The REALITY project aims to reuse aluminum from current Jaguar and Land Rover vehicles to incorporate it into new high-quality alloys, which will be used in the production of future vehicles.
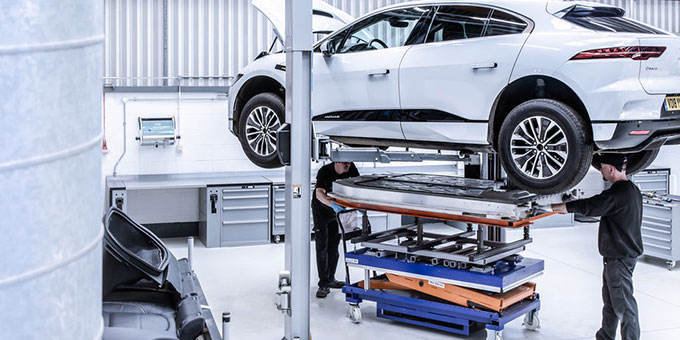
©Jaguar Land Rover
This process is currently being tested on pre-production Jaguar I-PACE prototypes, after dismantling their batteries. These incorporate their own new life process, developed by Jaguar Land Rover, when the last elements of the car are sorted by material family using high-tech Axion sensors. After separation, the aluminum pieces are melted down for reuse.
When operating at full capacity, REALITY will reduce the amount of CO2 emitted during the initial production of aluminum as well as the amount of virgin aluminum needed to manufacture vehicles. Jaguar Land Rover has already reduced the CO46 emissions linked to the production of its vehicles by 2% and remains committed to this decarbonisation process.
This pioneering project, co-financed by Innovate UK, allows Jaguar to extend the use of aluminum in closed circuits. Between September 2013 and January 2019, around 300 tonnes of recycled elements were reused for Jaguar's lightweight aluminum structure, which powers the entire range, including the XE.
In 2014, the Jaguar XE became the first car in the world to use RC5754 aluminum alloy for its body panels, which is made from 75% recycled aluminum. Half of the XE's body is made of alloys comprising a large part of recycled aluminum - this made possible by the closed-loop manufacturing process implemented at Jaguar Land Rover factories in the UK and Slovakia .
As part of an autonomous, connected, electric and shared future (also called ACES: Autonomous, Connected, Electric and Shared), many recycling opportunities will be enabled by the REALITY project, Jaguar Land Rover being able to foresee in advance the dismantling of large fleets of shared vehicles. The firm will thus be able to integrate closed-circuit recycling into its very dense production schedules, the vehicles being able to be recovered, decontaminated and dismantled en masse - this logically leading to the use of recycled aluminum by Jaguar Land Rover in its own. facilities.
Jaguar Land Rover uses 180 tonnes of aluminum annually. It is already one of the most recycled materials, with 000% of all aluminum produced since the end of the 75th century still in circulation today.
Over a million cars are crushed each year in the UK. This ambitious project allows us to give a second life to some of them. Aluminum is a valuable material and an important part of our manufacturing process. Thus, we are committed to using it in the most responsible way possible.
Gaelle Guillaume
Lead Project Manager, REALITY, Jaguar Land Rover
Recycled aluminum is put to the test by scientists at Brunel University, who perform stress tests and verify its quality to ensure that it meets the mechanical standards necessary for use in Jaguar and Land bodies. Rover.
Rallye des Princesses: 5th and last stage in La Baule
Rallye des Princesses Richard Mille 2022: summary of stage 4
Rallye des Princesses 2022: the highlights of stage 2
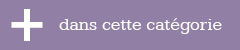